ICs are at the heart of modern electronics: from your smartphone to your pacemaker, all work thanks to an IC. Do you know, though, that these miniature chips are quite sensitive to damage? An electrostatic discharge as small as ESD can even cause the ruin of an IC before it ever leaves the manufacturer for a customer. PVC IC tube packaging steps into this picture and plays a role in shielding the sensitive component.
In this blog, we’ll break down how anti-static IC tubes in India safeguard ICs from damage and why they’re the preferred choice for manufacturers.
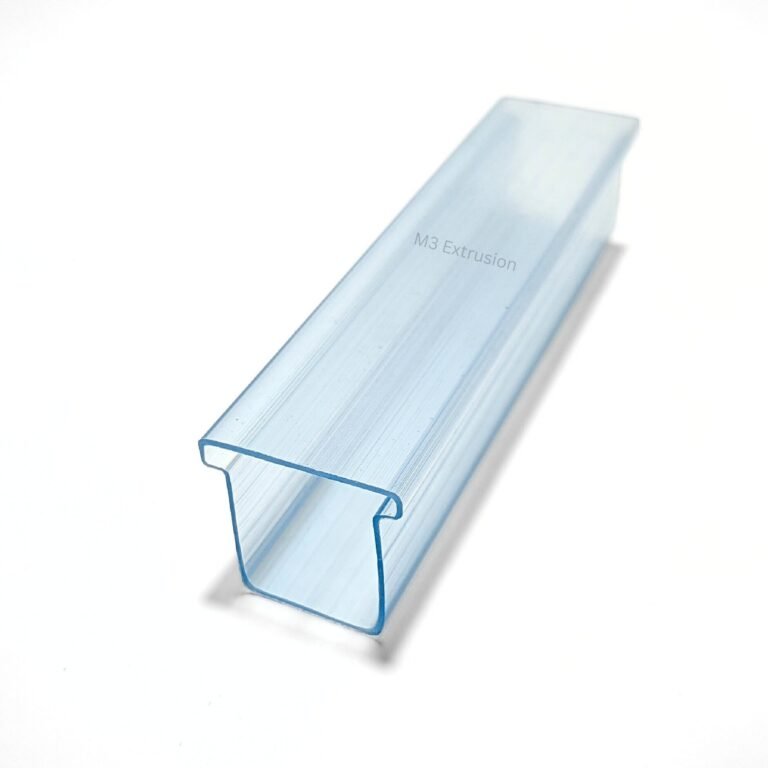
Why Are Integrated Circuits So Fragile?
Before we delve into packaging solutions, let’s understand why ICs require protection. Integrated circuits consist of mini-electrical pathways; disruption by the following events can occur easily:
- Electrostatic Discharge: Just one touch could generate thousands of volts of static electricity, frying an unprotected IC instantly.
- Moisture Damage: Humidity causes corrosion, which affects circuit performance and longevity.
- Mechanical Effect: Even slight vibrations or impacts can lead to micro-level breakages in the chip structure.
- Dust & Impurities: Tiny dust particles can cause short circuits and malfunction.
Now that we are well aware of the above risks let us now see how PVC IC tube packaging overcomes all these complications.
How PVC IC Tube Packaging Protects Integrated Circuits?
1. Anti-Static Protection to Avoid ESD Damage
Electrostatic discharge is one of the major threats to ICs. Anti-static IC tubes are used to neutralize static electricity. They prevent any harmful charges from building up in the circuits, which may cause damage.
- The tubes are made from PVC material infused with anti-static properties, which dissipates static energy safely.
- They also ensure that ICs do not rub against each other, thus reducing friction that may generate static.
- Many manufacturers prefer anti-static IC tubes over other packaging options like trays because they offer consistent ESD protection throughout handling and transportation.
2. Tight Fit for Mechanical Protection
ICs are tiny and fragile. Any movement in transport may result in scratches or bent pins. Custom plastic tubes are designed to provide a snug fit so that ICs will not shift around inside.
- The rigid PVC structure will not allow the ICs to be damaged if the package is dropped.
- Loose packaging materials are prone to pin bending, which is a common problem in IC handling. These tubes do not allow accidental pin bending.
3. Easy Storage and Handling
Manufacturers need packaging that protects ICs and makes storage and handling easier. PVC IC tube packaging is convenient:
- Stackable and Space-Saving: Unlike bulky plastic trays, tubes can be neatly stacked, saving storage space.
- Transparent for Easy Identification: Many PVC tubes are clear or semi-transparent, allowing workers to quickly identify the ICs inside without opening them.
- Lightweight Yet Sturdy: PVC tubes provide strong protection while being much lighter than alternative packaging materials like metal or thick plastic trays.
4. Customization for Different IC Sizes
Not all ICs are of the same size. Thus, one type of packaging does not fit all, and that’s where custom plastic tube packaging is crucial. Here are some advantages manufacturers can expect with customized PVC IC tubes so they fit chip dimensions perfectly to avoid:
- Shifting movement inside the tube.
- Chipping of pins in IC
- Ease automation. The whole process of the ICs in a robotic pick-and-place machine will be streamlined.
- This level of personalization makes PVC tubes suitable for mass production and global shipping.
Why is PVC the Best Material for IC Tube Packaging?
You would probably wonder why PVC and not some other material? Here’s why PVC happens to be the industry favorite:
- Cost-Effective: PVC happens to be cheaper than alternatives, such as polycarbonate or acrylic.
- Durable: It resists pressure and does not break easily, thus holding ICs intact.
- Chemical Resistant: PVC does not react with most chemicals, thereby providing a clean and contaminant-free environment for ICs.
- Flexible: It can be molded in any shape and size, thus ideal for customized plastic tube packaging.
These characteristics make PVC ideal for long-term protection of integrated circuits.
Conclusion
One of the most reliable solutions when it comes to protecting integrated circuits is PVC IC tube packaging. It provides the best anti-static IC tube protection, guarantees a secure fit, simplifies handling, and can be customized according to the different sizes of chips.
Manufacturers seeking quality IC packaging solutions may look for them at M3 Extrusion, which is a reputable provider of custom plastic packaging.
Choosing the right packaging ensures that your ICs are protected from damage while also ensuring that the manufacturing and delivery processes go smoothly. To protect your electronics, PVC IC tubes are the best!